The adaptable Kurt RV36 Robotic Arm Gripper offers patent-pending design in a powerful, cost-effective package.
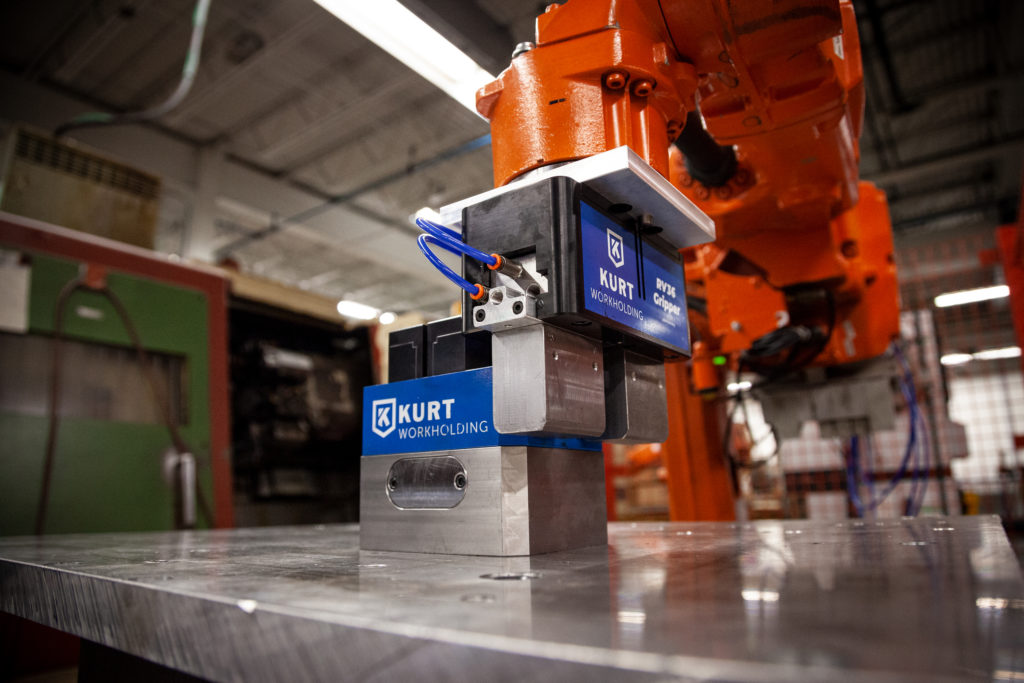
The Kurt RV36 Gripper is the only robotic gripper with quick-change customizable fingers, thus saving you time, space and money. Because there is no need for expensive interface plates and no need to change gripper bodies to pick up and handle multiple part configurations, a single gripper body can perform many different tasks.
Gripper fingers are swappable and machinable
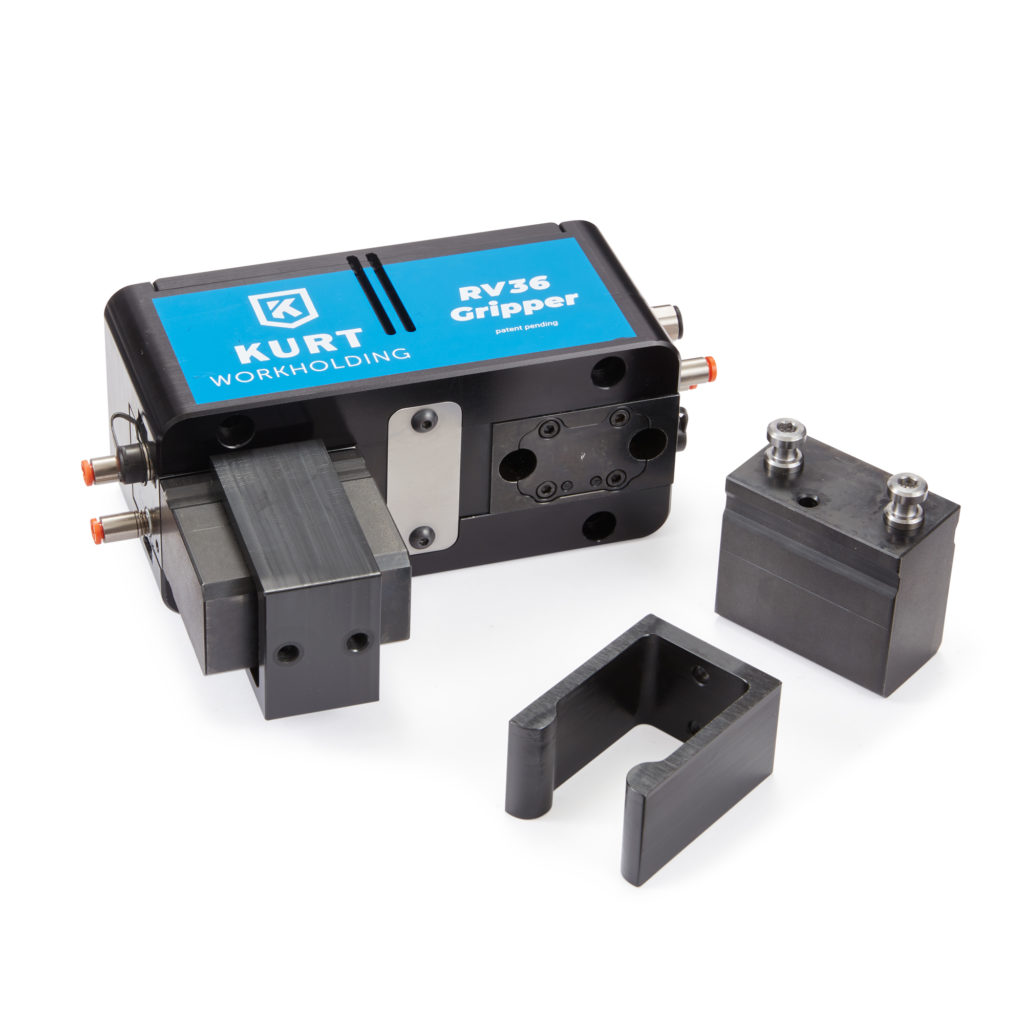
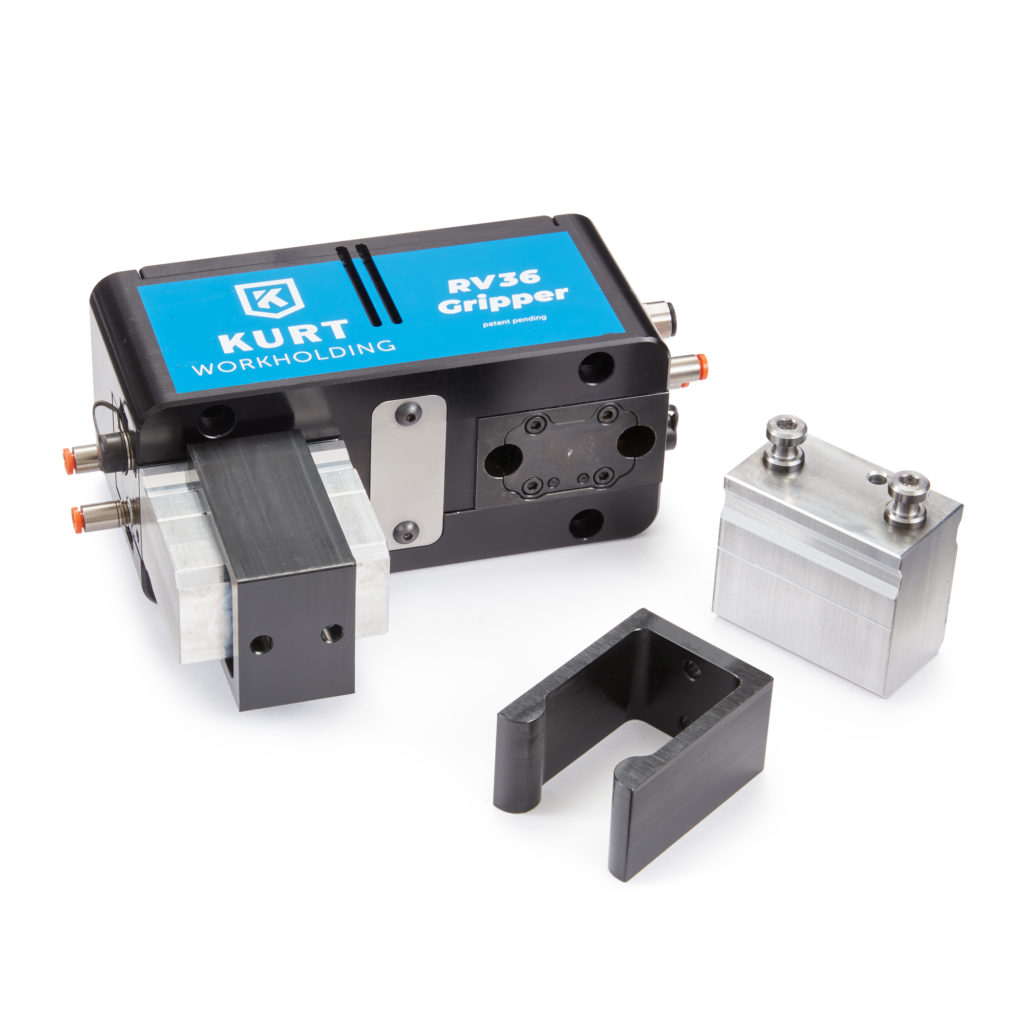
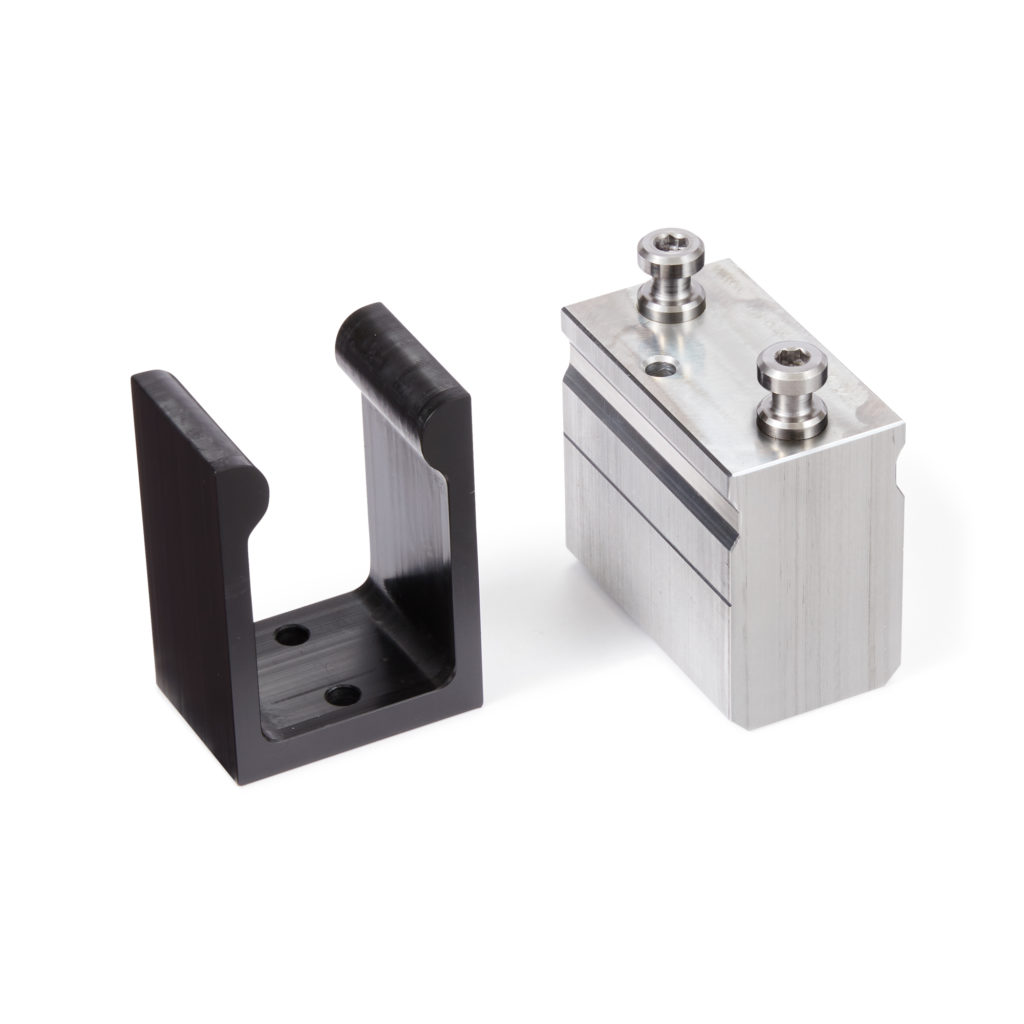
Kurt offers machinable aluminum and steel finger sets with pull studs that attach to the gripper body using pneumatic pressure. Gripper fingers have a .6-inch stroke length. To match the shape of the part you need to pick up with the robot, fingers can be machined, allowing grippers to be customized to fit many varied applications. The line on the side of the finger marks how much material can be removed from the fingers without damage, similar to the approach we use with Kurt machinable vise jaws. Gripper fingers can be machined to fit any application as long as safe machining areas are maintained and the project fits within specified limits of the RV36 and the robot.
Total workholding versatility
Pull-stud equipped, quick-change fingers allow a robot to go from manipulating a large casting with custom fingers to picking up a slip sheet with a vacuum gripper without manual intervention. Gripper finger options can be positioned high to save space in a work cell with only a single gripper body is needed for multiple setups.
Click the image to watch the video –>
A powerful robotic vise with quick-change fingers
Even without the revolutionary quick-change design, the RV36 Gripper is a powerful, multipurpose end effector for those who may never use the quick finger change feature. The gripper itself works very much like a small vise with a double-acting pneumatic cylinder controlling jaw and thus finger positioning. With air pressure applied to either side, the double-acting cylinder ensures quick and dependable jaw movement. With the addition of the optional magnetic sensors, the cylinder position can be monitored to assure that the jaws are in the desired position.
Each pull stud provides 1,000 pounds of retention force on secured fingers, meaning it takes 1,000 pounds of force to pull out a gripper finger. Pull stud release and engagement occurs with actuation at the robot through connected I/O.
Accessory sensors and finger racks
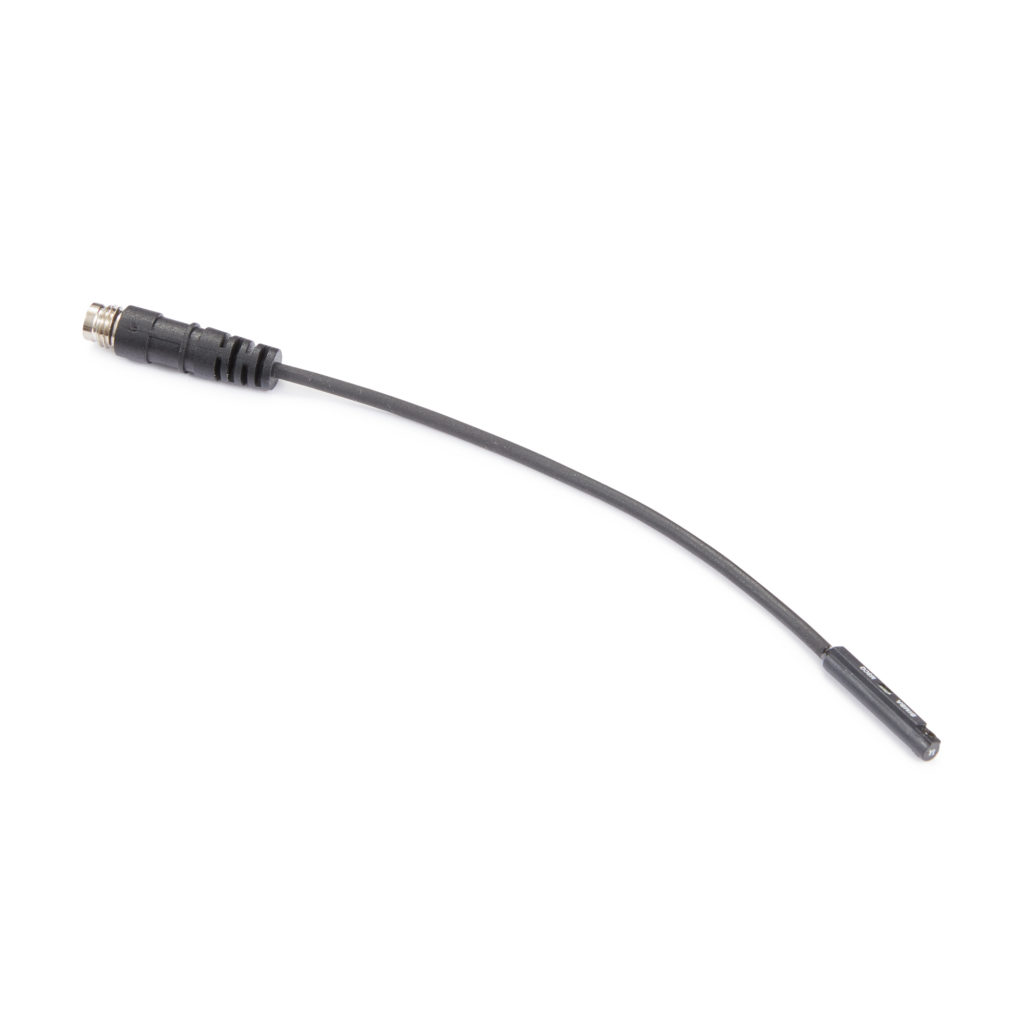
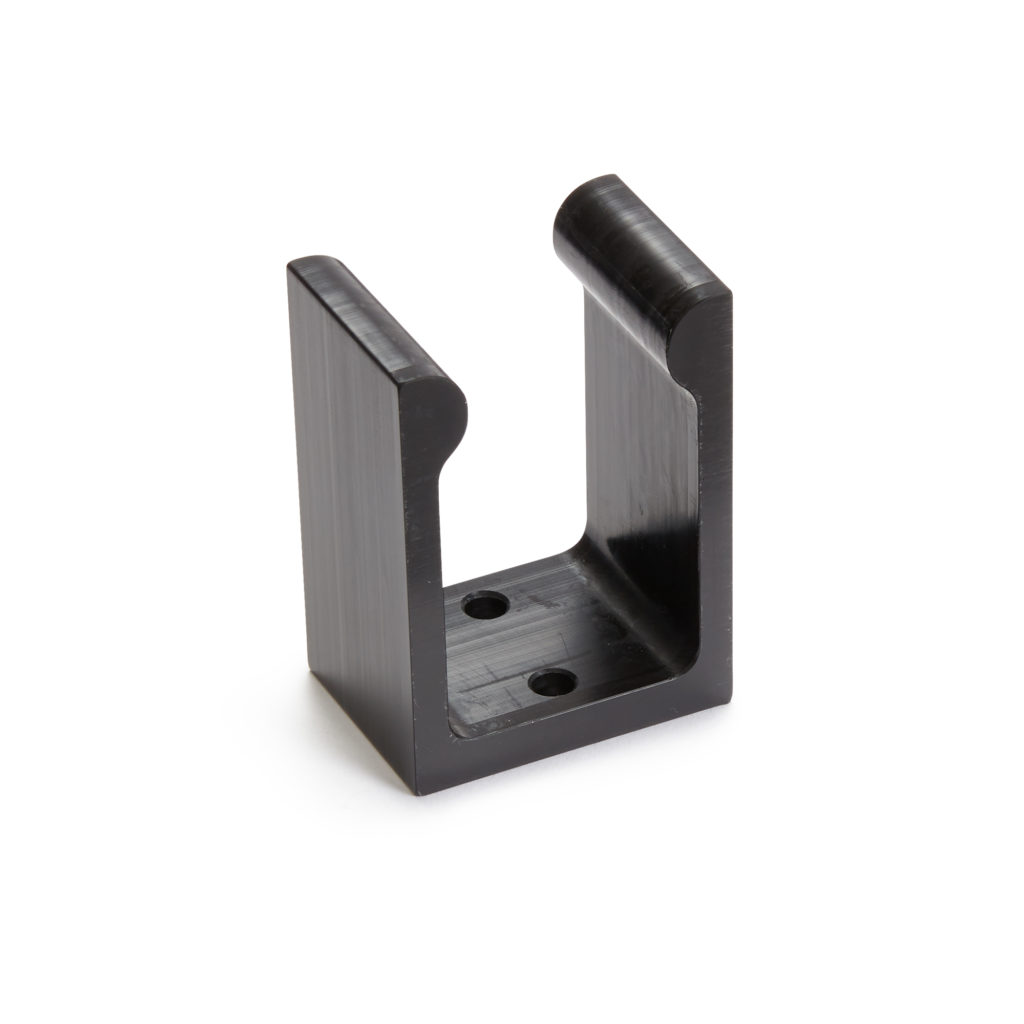
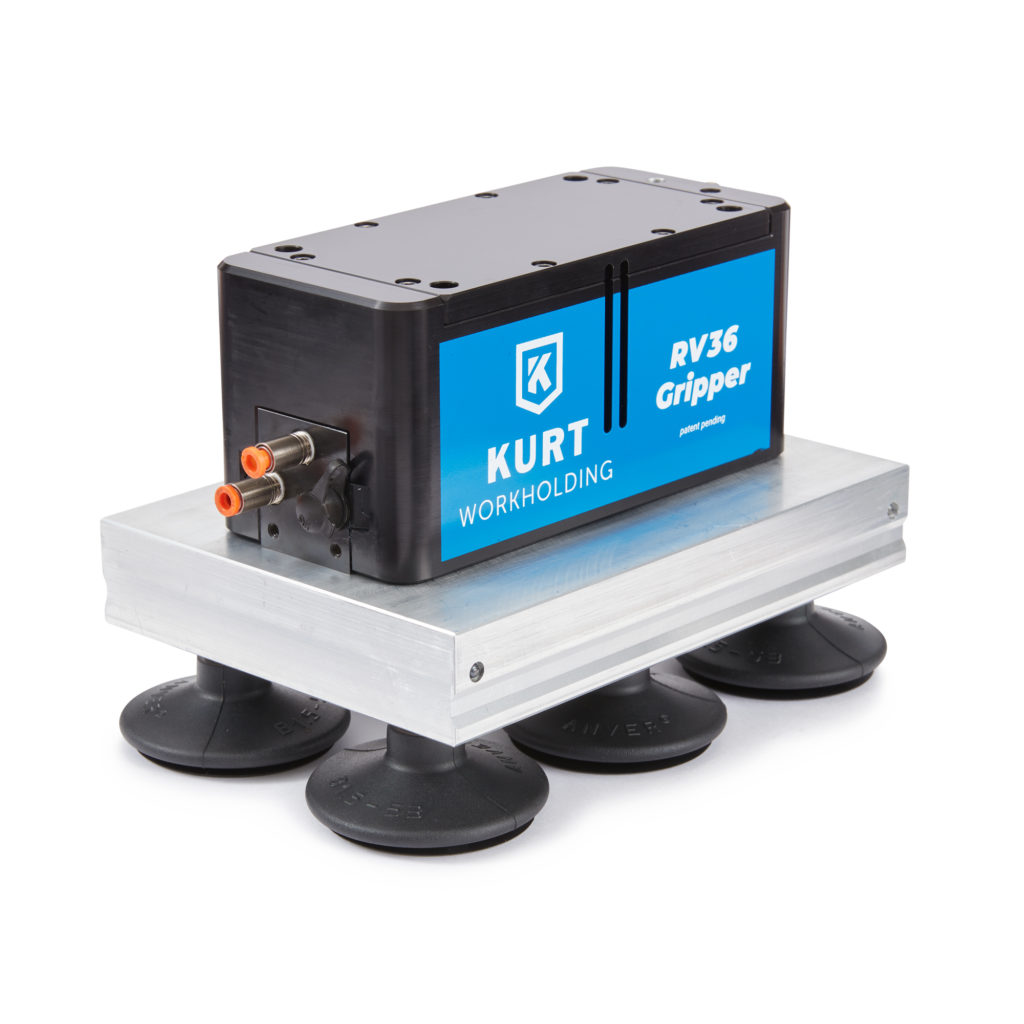
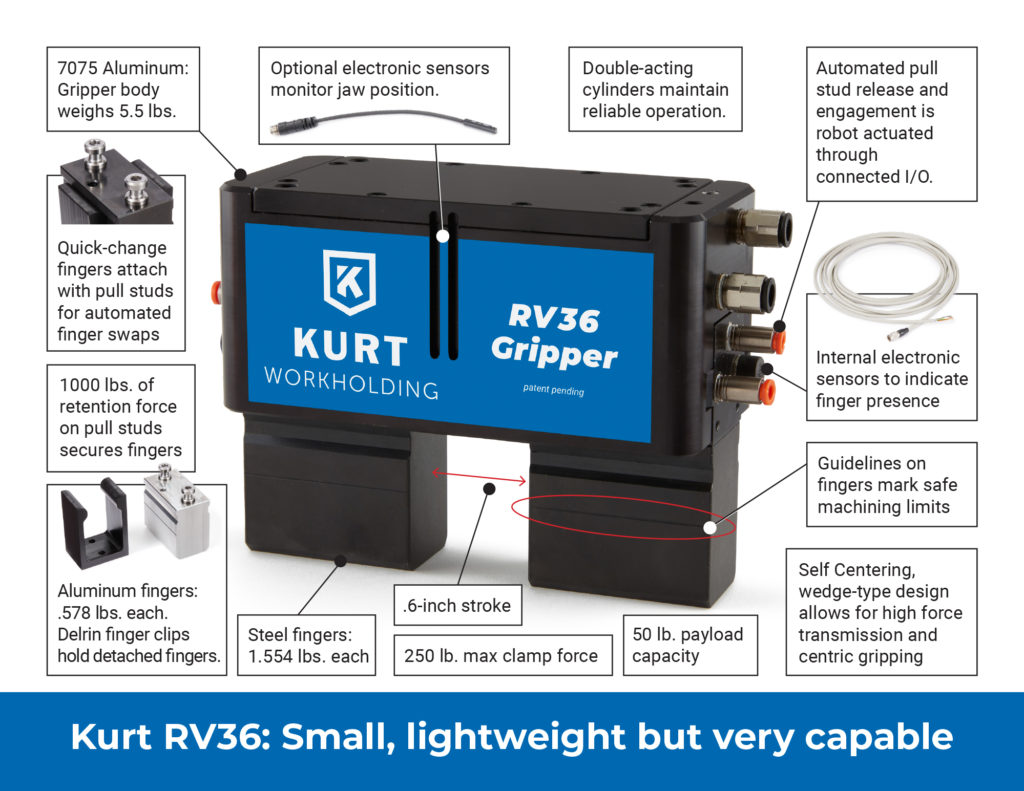
Other features include monitoring sensors embedded in the body for determining when the gripper is open or closed. Optional sensors can also be run through the fingers to sense if a part is or isn’t in the gripper.
Delrin finger racks are also available to release and capture fingers during end-effector changes. As demonstrated in the video above and the images below, you can go from manipulating a large casting with custom fingers to picking up a slip sheet with a vacuum gripper without manual intervention.
Kurt grinder cell automation with RV36 Gripper
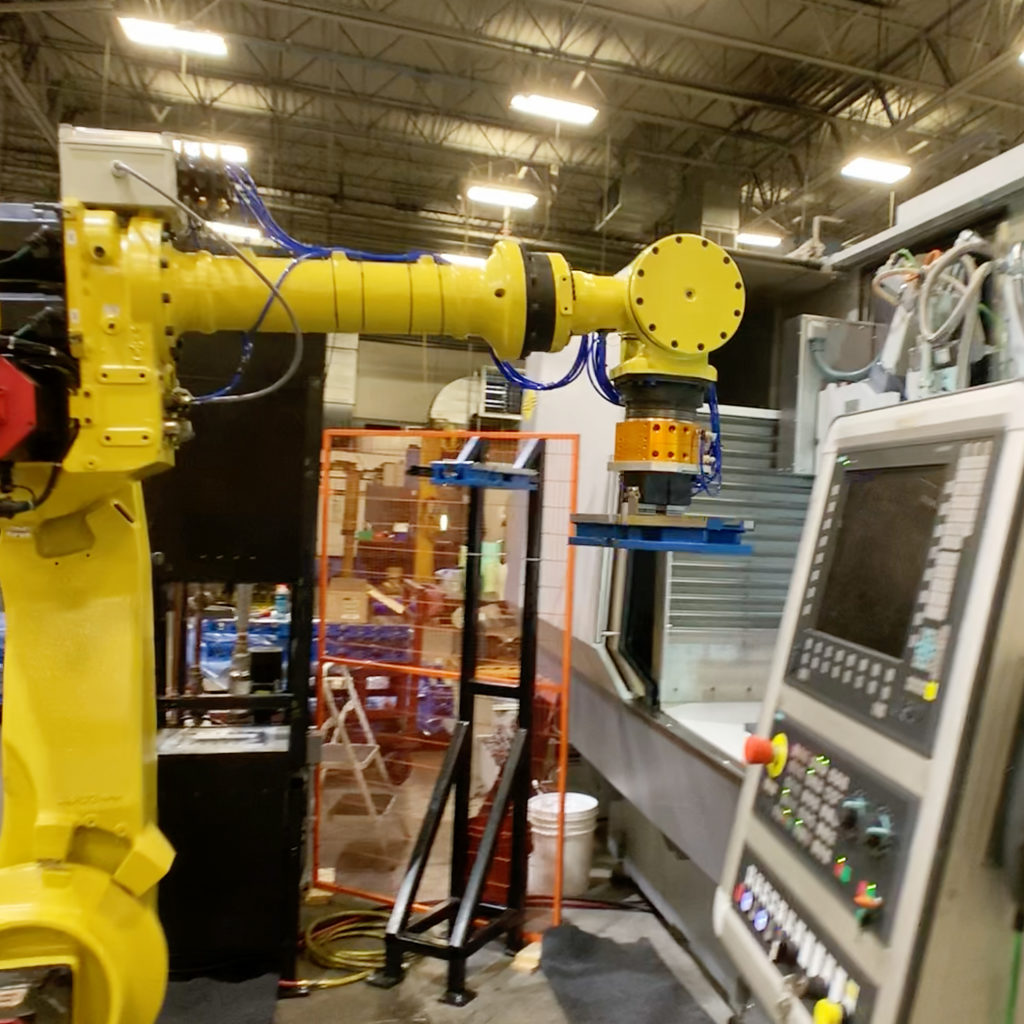
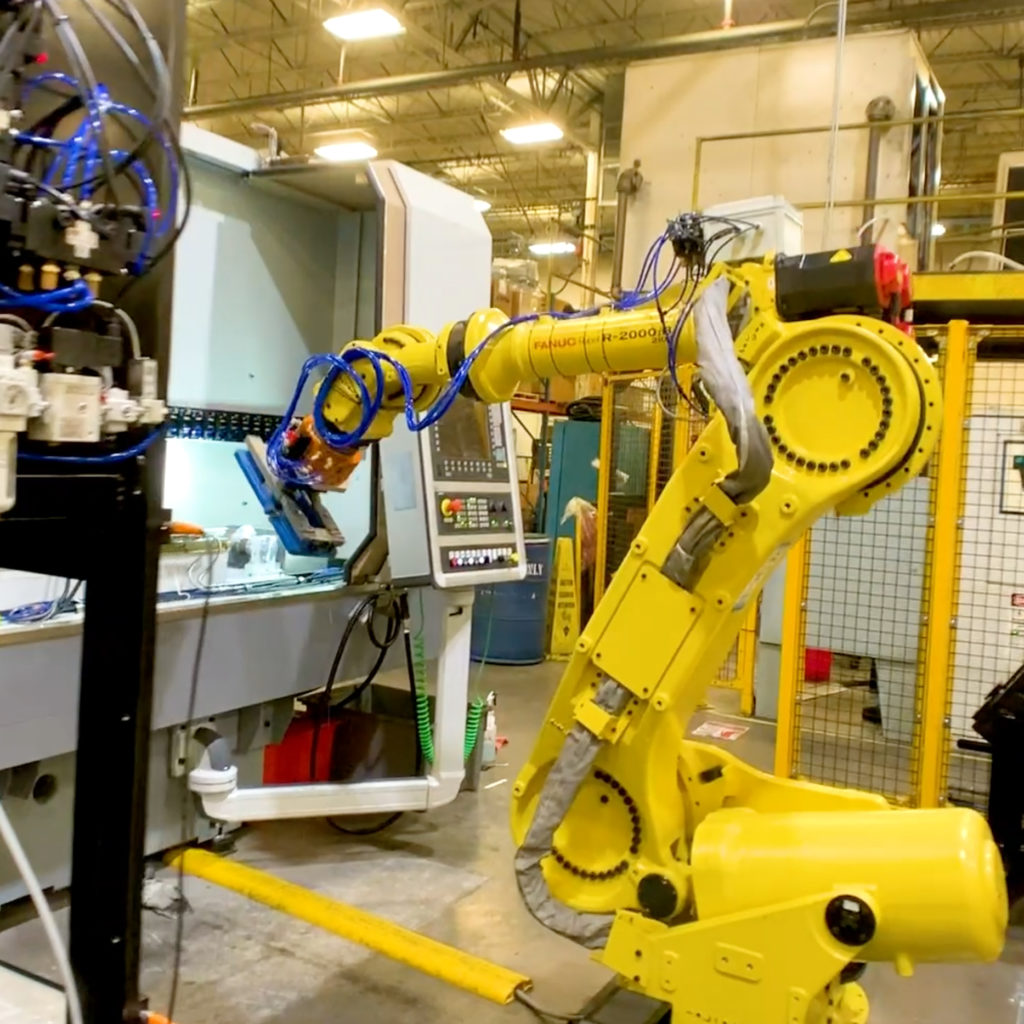
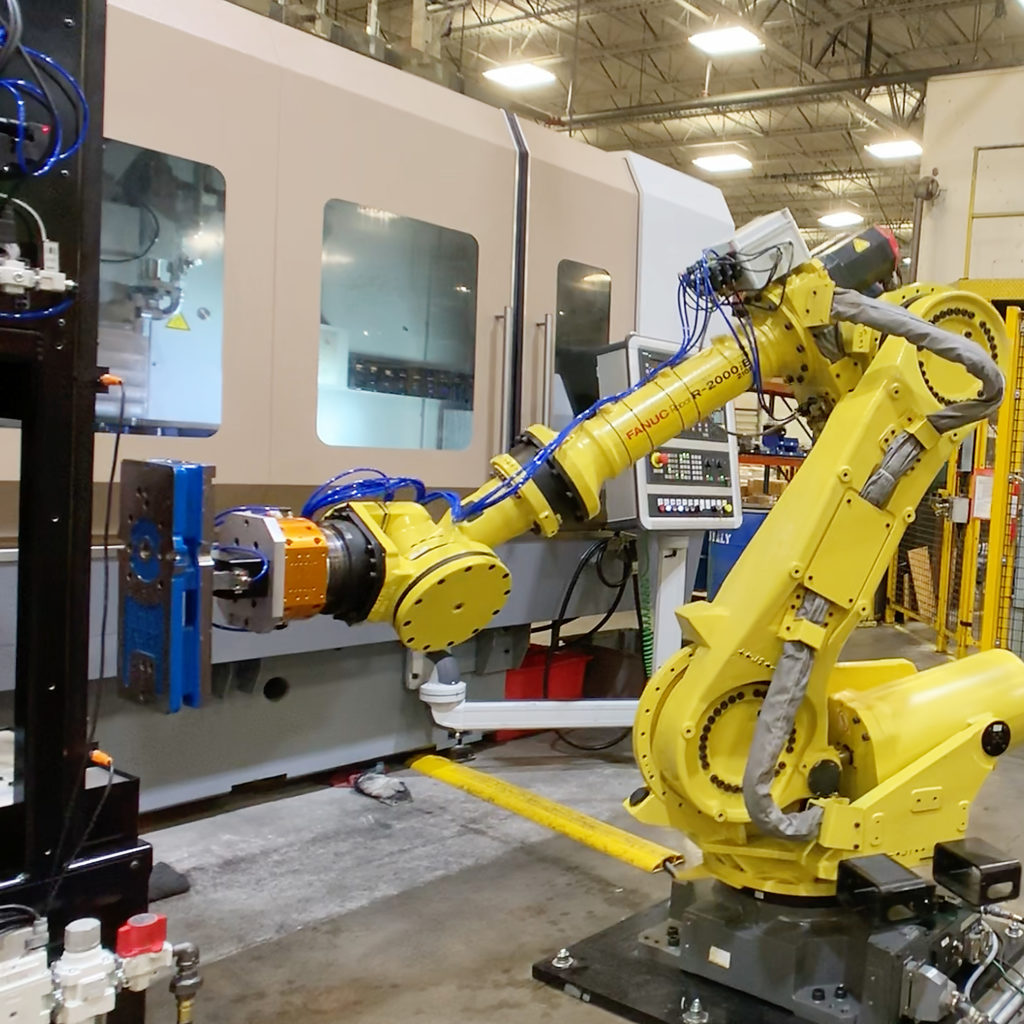
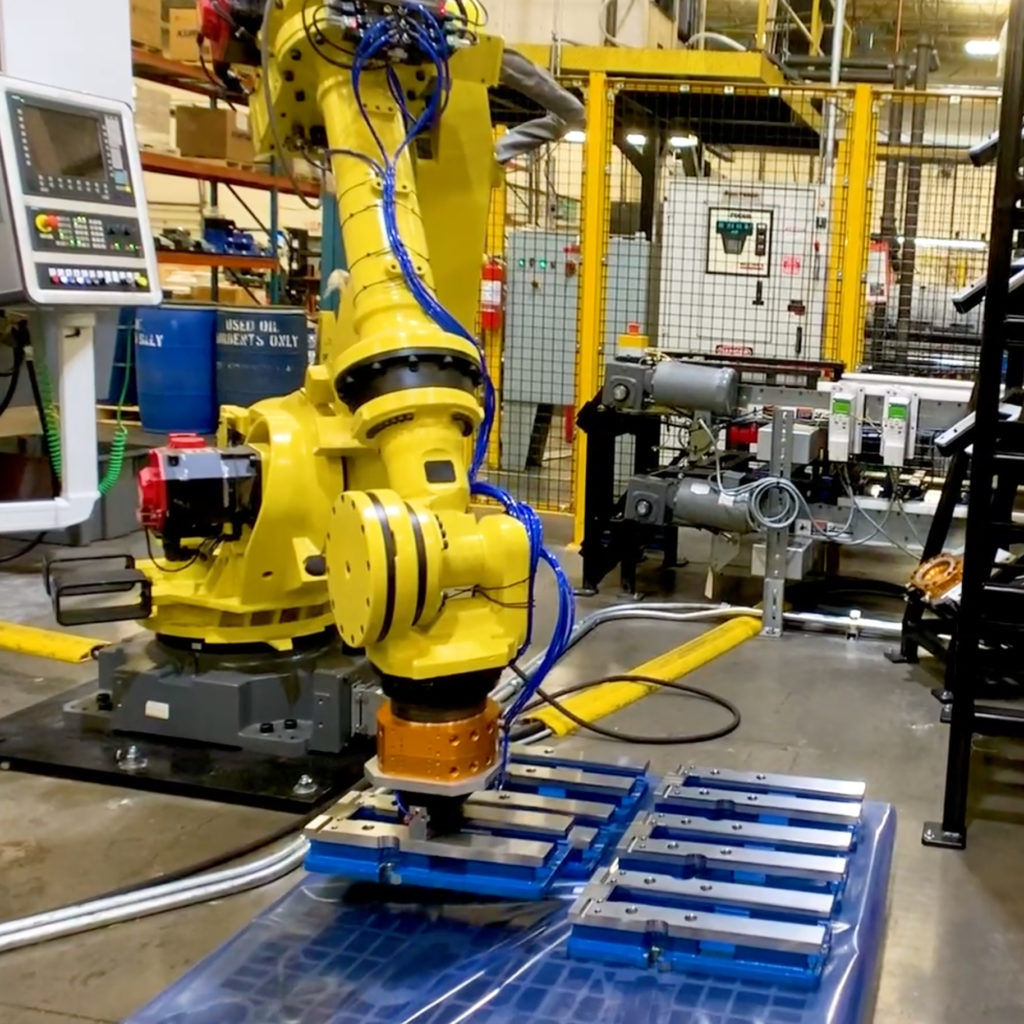
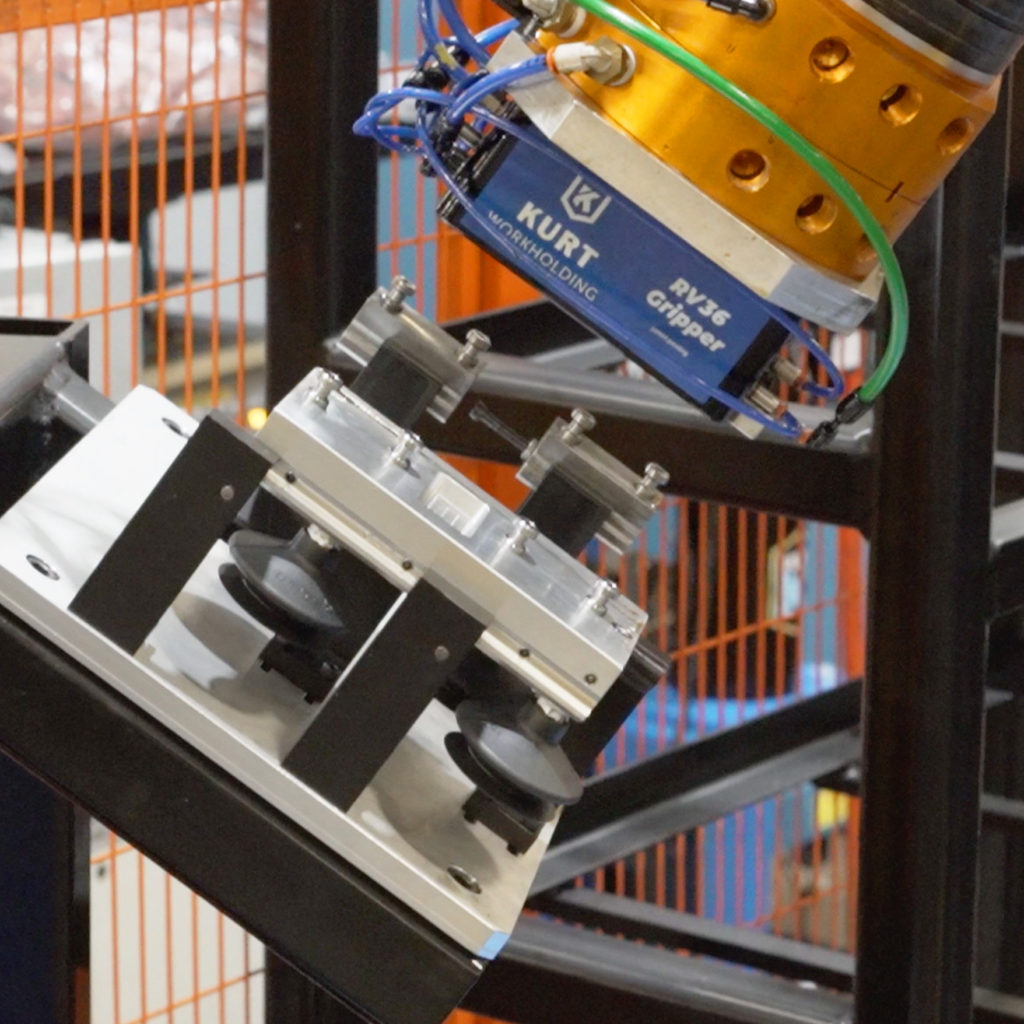
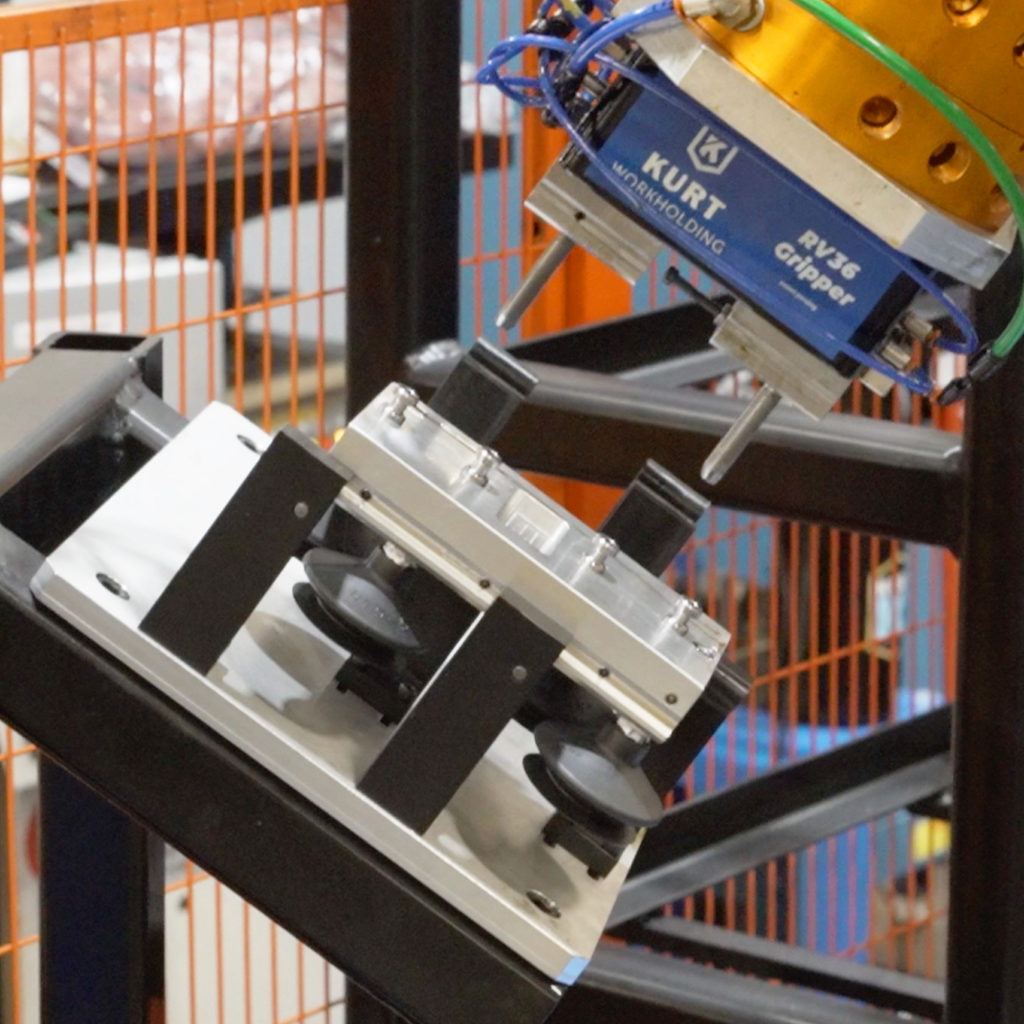
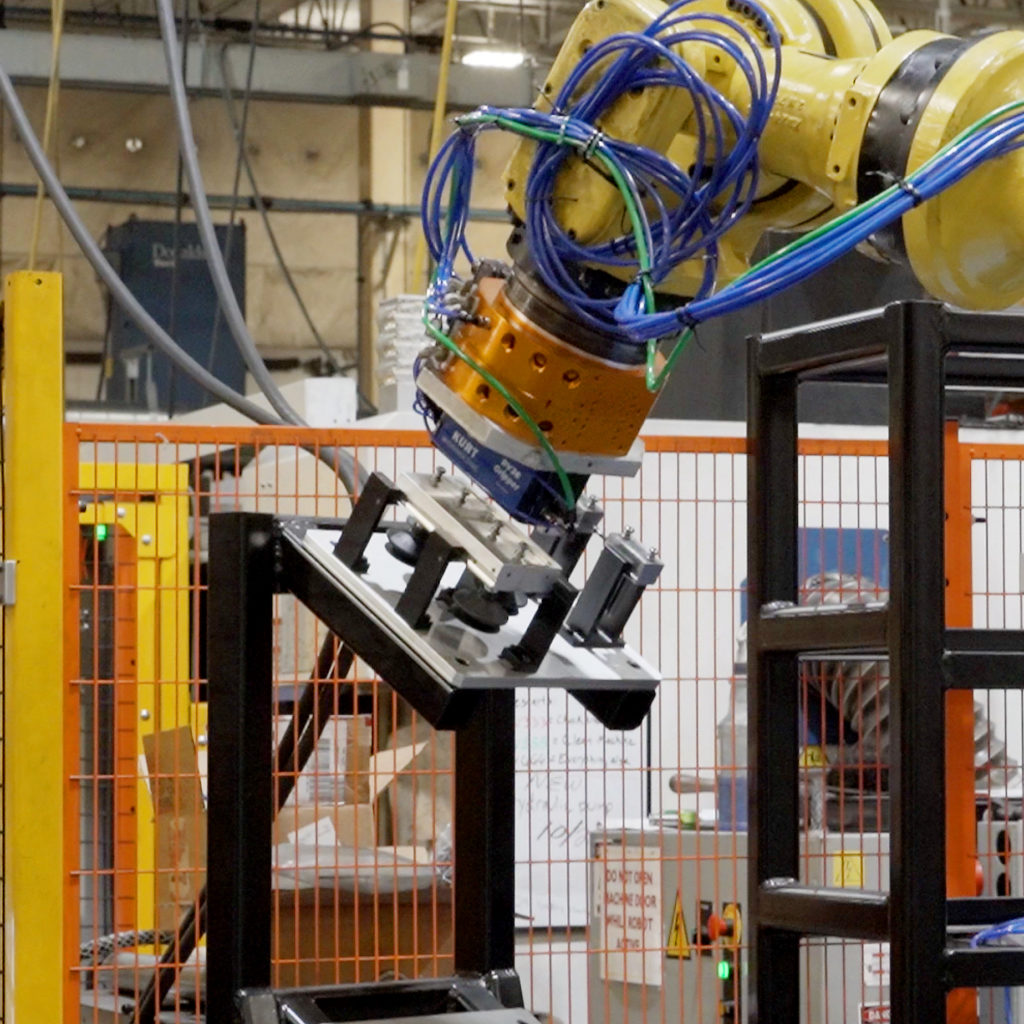
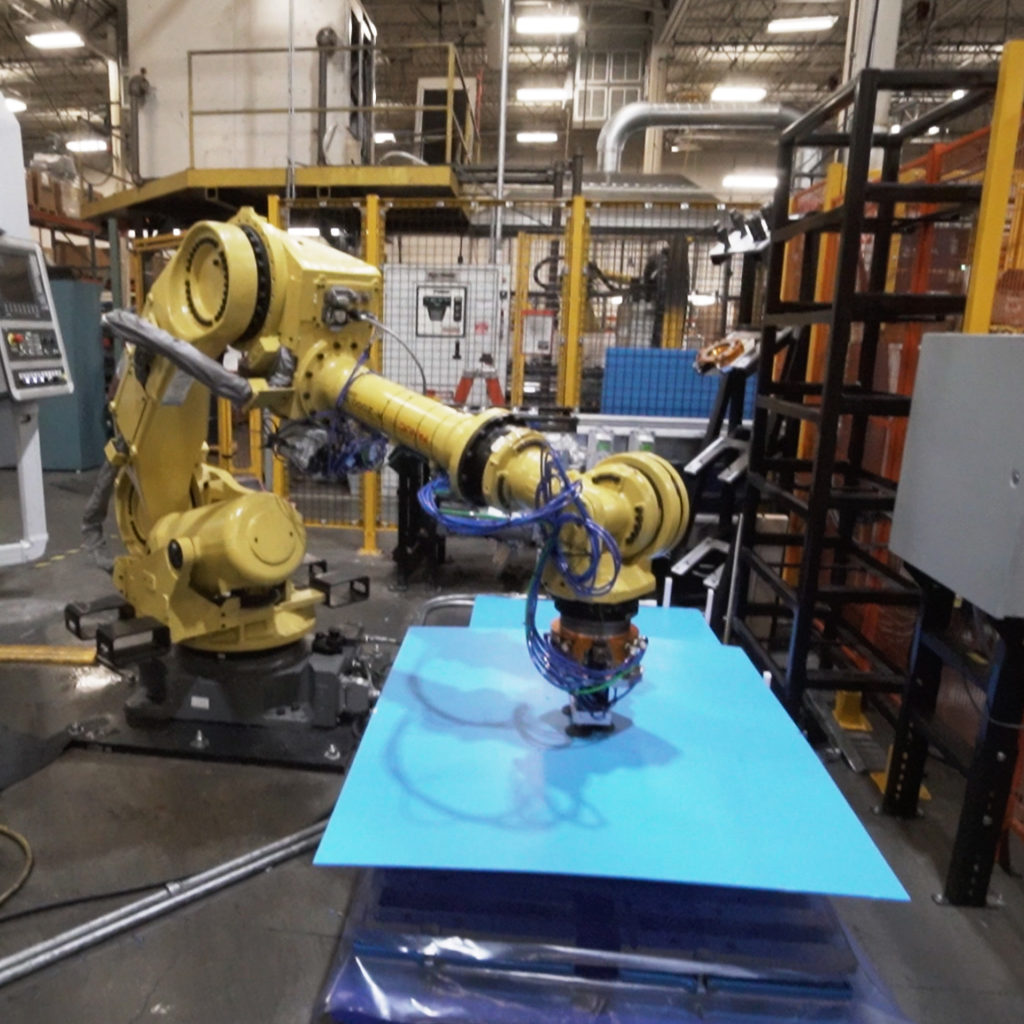
Compact size meets payload power
At just under six pounds with the standard aluminum jaw configuration and a 50-pound payload, the, the RV36 Gripper packs a lot of power for its compact size and big savings for your automation budget. Contact us and we’ll help you integrate the Kurt RV36 Gripper into your workflow.
Workholding versatility like no other gripper (video below)
Or Contact Us for more information about a specific project.
Check out our Kurt Innovative Demo Partnership Program