An early CARVESMART customer, Laitram uses the quick-change dovetailed jaw system to cut their job setup times in half.
Kurt recently traveled to New Orleans and went behind the scenes at Laitram Machine Shop, a top-level Kurt with CARVESMART customer. With a global reach and 70 years of experience, Laitram is a leading manufacturer of seafood processing equipment, cookers, blanchers, nut processing equipment, and conveyor systems designed to automate package handling. An early CARVESMART customer, Laitram found the dovetailed quick-change jaw system when seeking a way to cut their job setup times in half. As part of a push for operational excellence, they were examining ways to optimize their manufacturing processes and to carve expenses and wasted time out of their systems. Setup times were taking nearly 7 hours per job, and they challenged themselves to try and cut that in half.
“With the help of the CARVESMART dovetailed master jaw system they were able to get that setup time down to just 2.5 hours per job!” said Ted Matherne, Manufacturing Specialist at Laitram Machine Shop. “We also integrated a grid system that along with CARVESMART, helps get ‘first part, good part’ results.”
Ted showed our sales and marketing team around the shop where we saw many machines running jobs using Kurt vises including, two Kitamuras and a Haas VF10 running. Two of the machines featured 14 vises mounted side-by-side to hold 10-foot-long strips of plastic that were being machined into guide rails for Intralox conveyor systems—another Laitram division. A combination of Kurt HD690 and 3600V 6-inch vises share the workholding duties on those machines using CARVESMART Master Jaw Sets for quick jaw changes and machine setups. They purchase their soft jaw extrusions in bulk from Kurt and cut them to fit the part for every setup.
One of the advantages of using CARVESMART jaws for quick changes is that Laitram can use a CARVESMART hardened knife edge jaw for the first op to hold extra part material for facing, profiling, and machining the most critical features—then quickly change jaws to carved aluminum soft jaws for the flip operations. “We mill the part profile into the aluminum soft jaws to face what we were holding in first ops, then complete machining on the remaining features,” said Matherne. “A benefit is not setting a part origin on the first operation since it’s dedicated—we reference where to load by using an engraved scale on face of the hard jaw.”
Take a look at how Laitram Machine Shop integrated Kurt with CARVESMART vises and master jaw sets into their shop.
Laitram makes use of a jaw recycling system where each soft jaw set gets used 3 times before it’s scrapped. They use a set of soft jaw on one job and then machine them down into a smaller profile and recycle the jaws for another job. This allows a single set of soft jaws to last 3 to 4-times longer. When that job or setup is finished, they put the used CARVESMART jaws into a bin to be used again after getting milled down to a new smaller profile. A jaw can typically be used 3 to 4 times before it’s recycled. Each time a jaw has been used in a job and goes to the recycling carts; an operator checks the profile against a chart that shows the next size the jaw will be milled into and places the jaw in that cart.
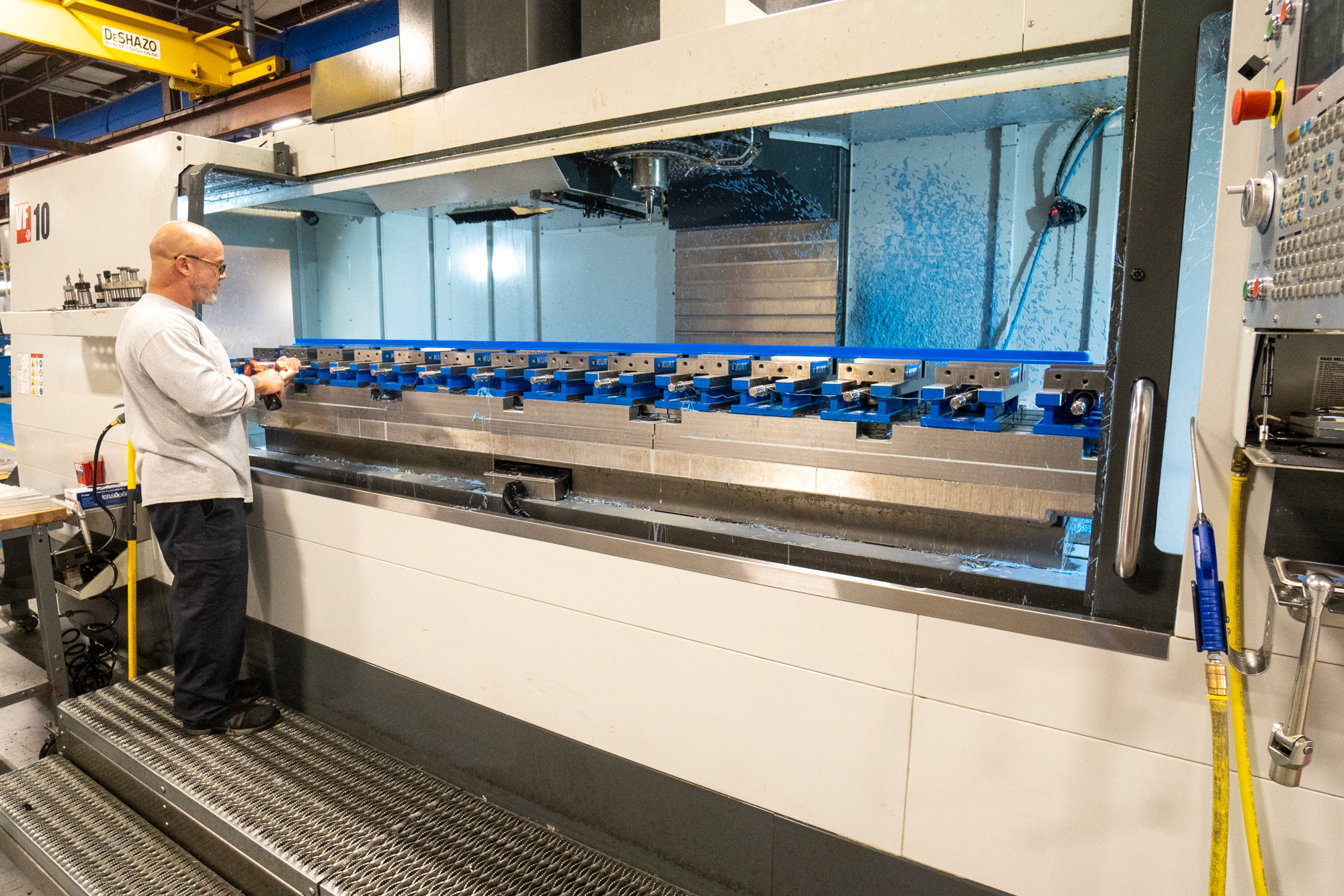

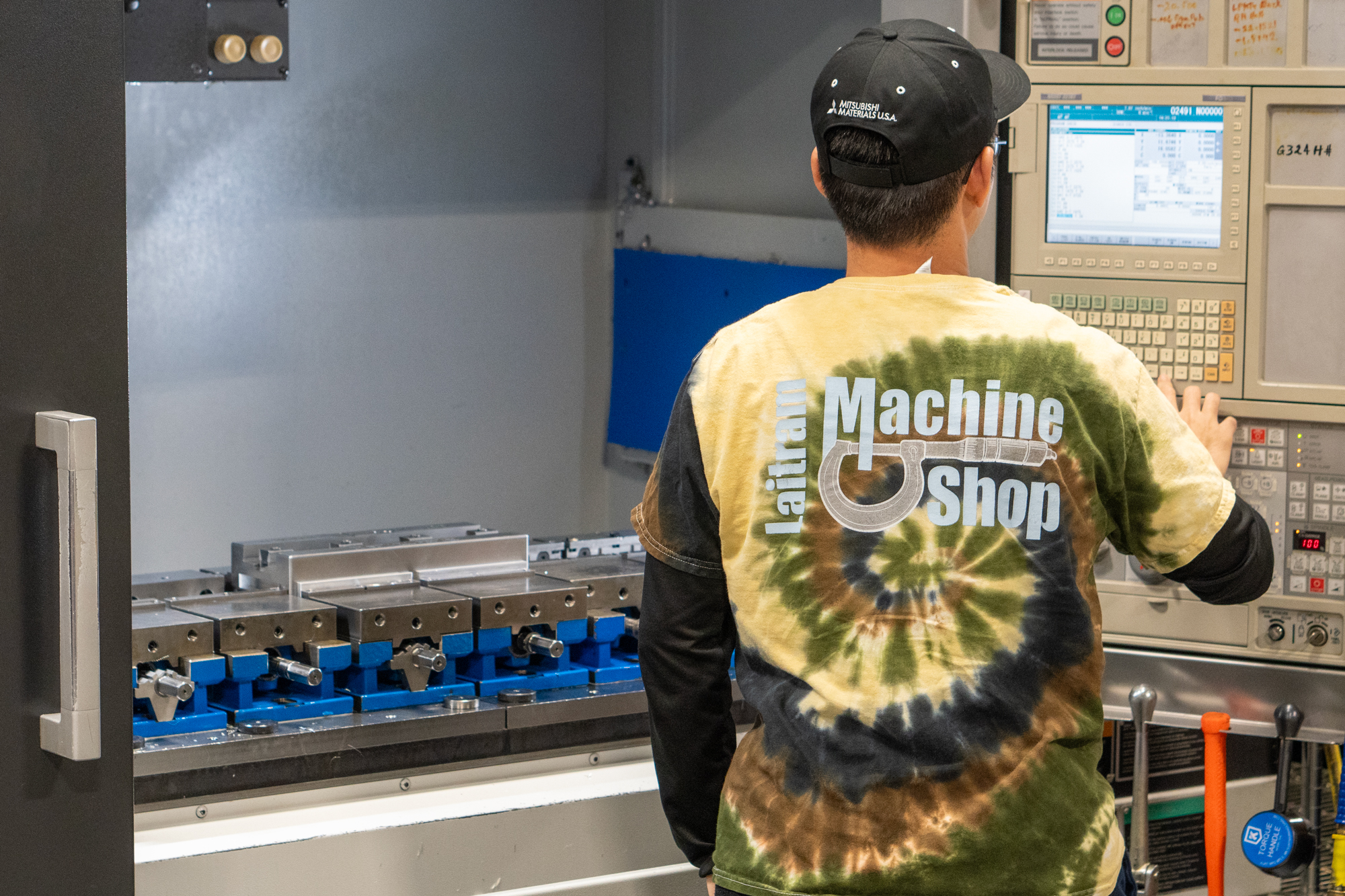
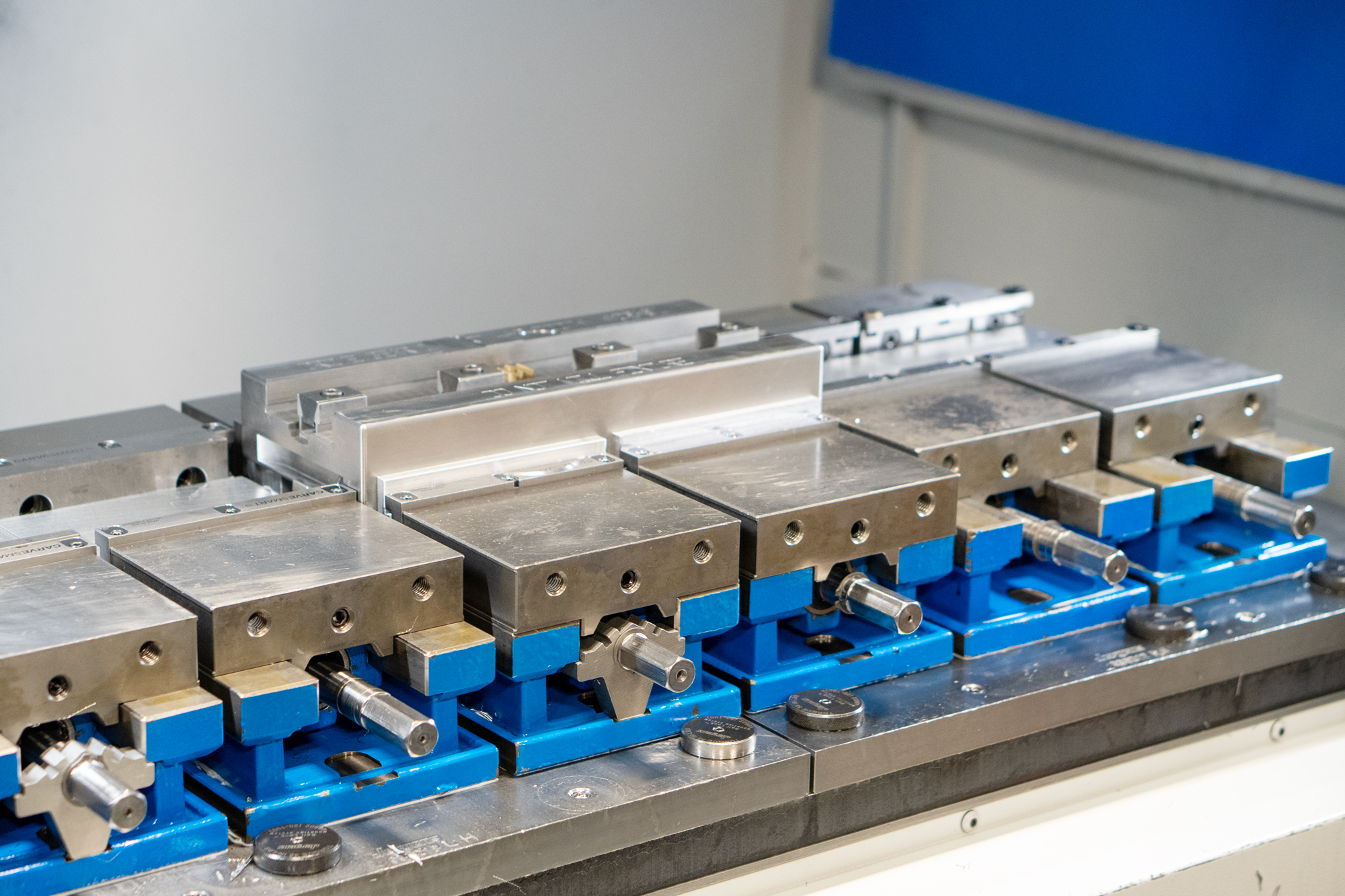
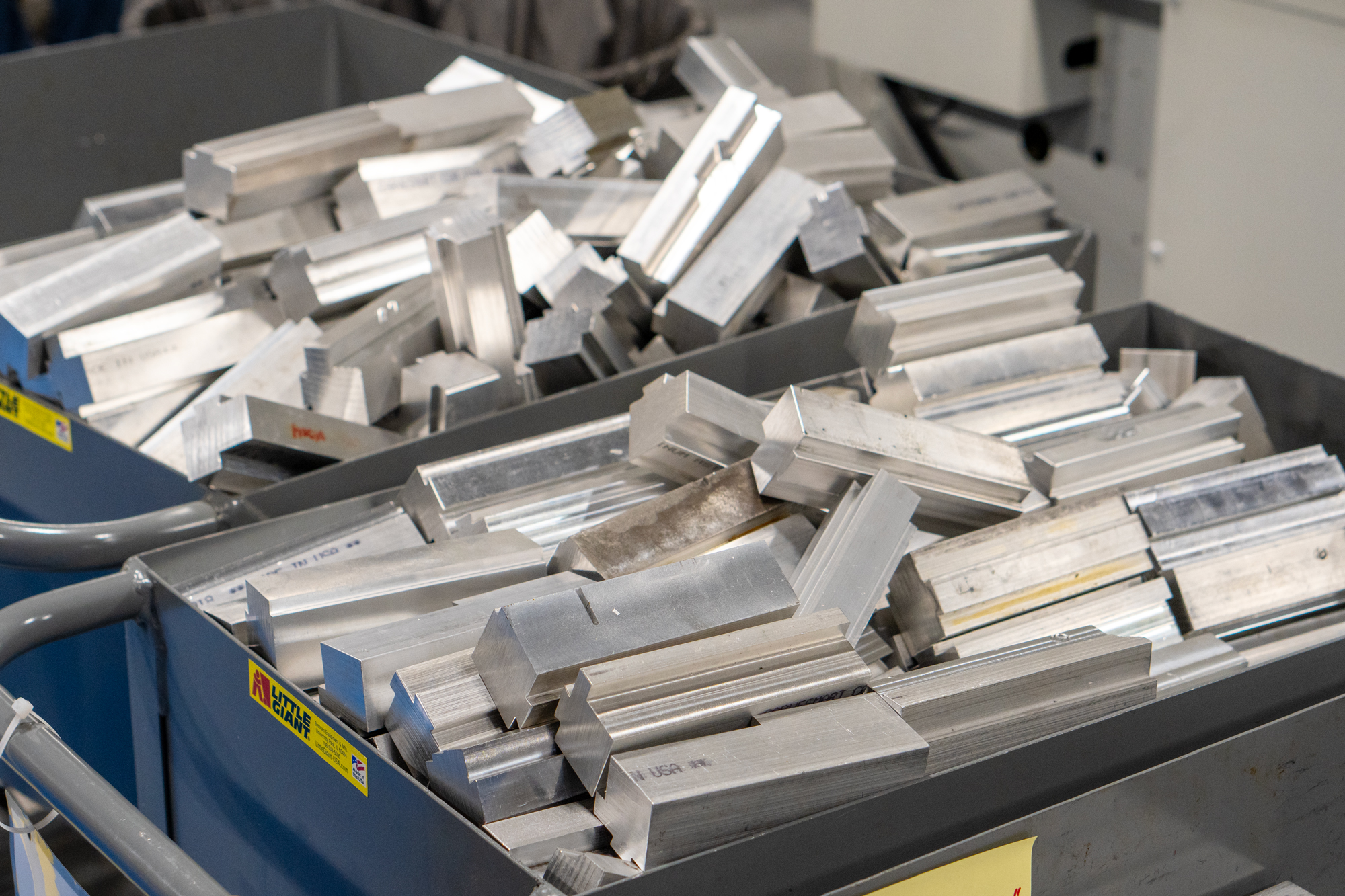
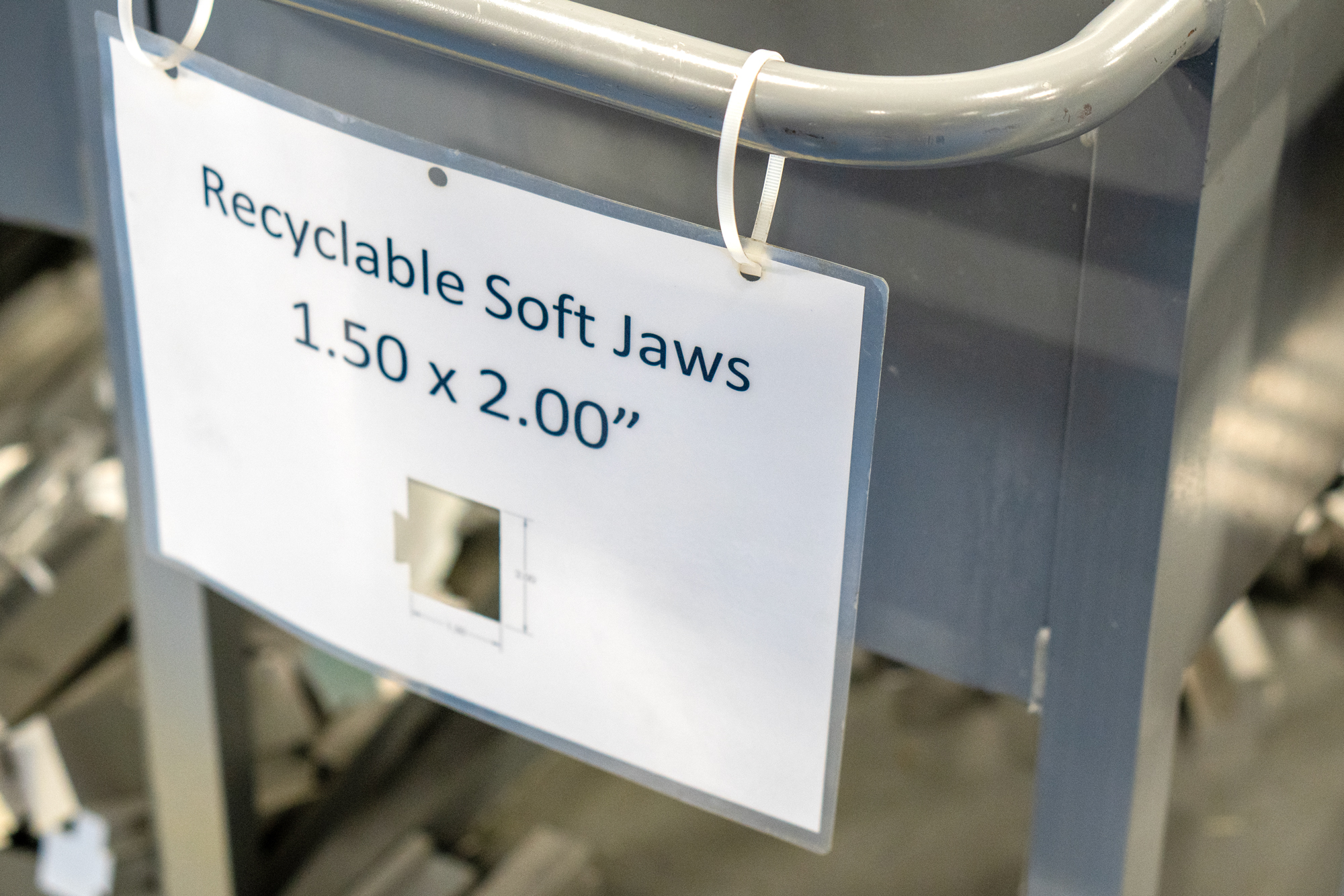

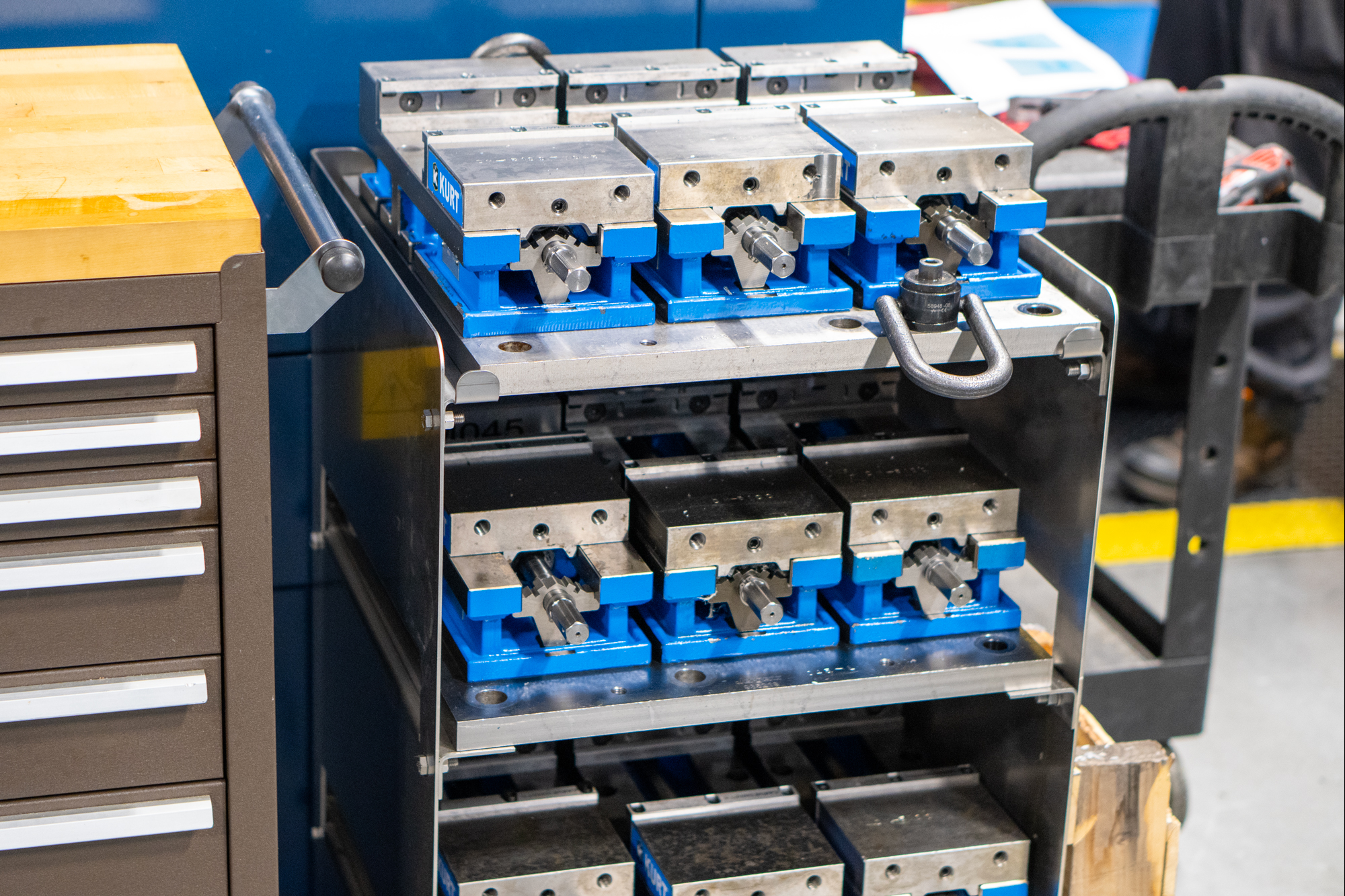
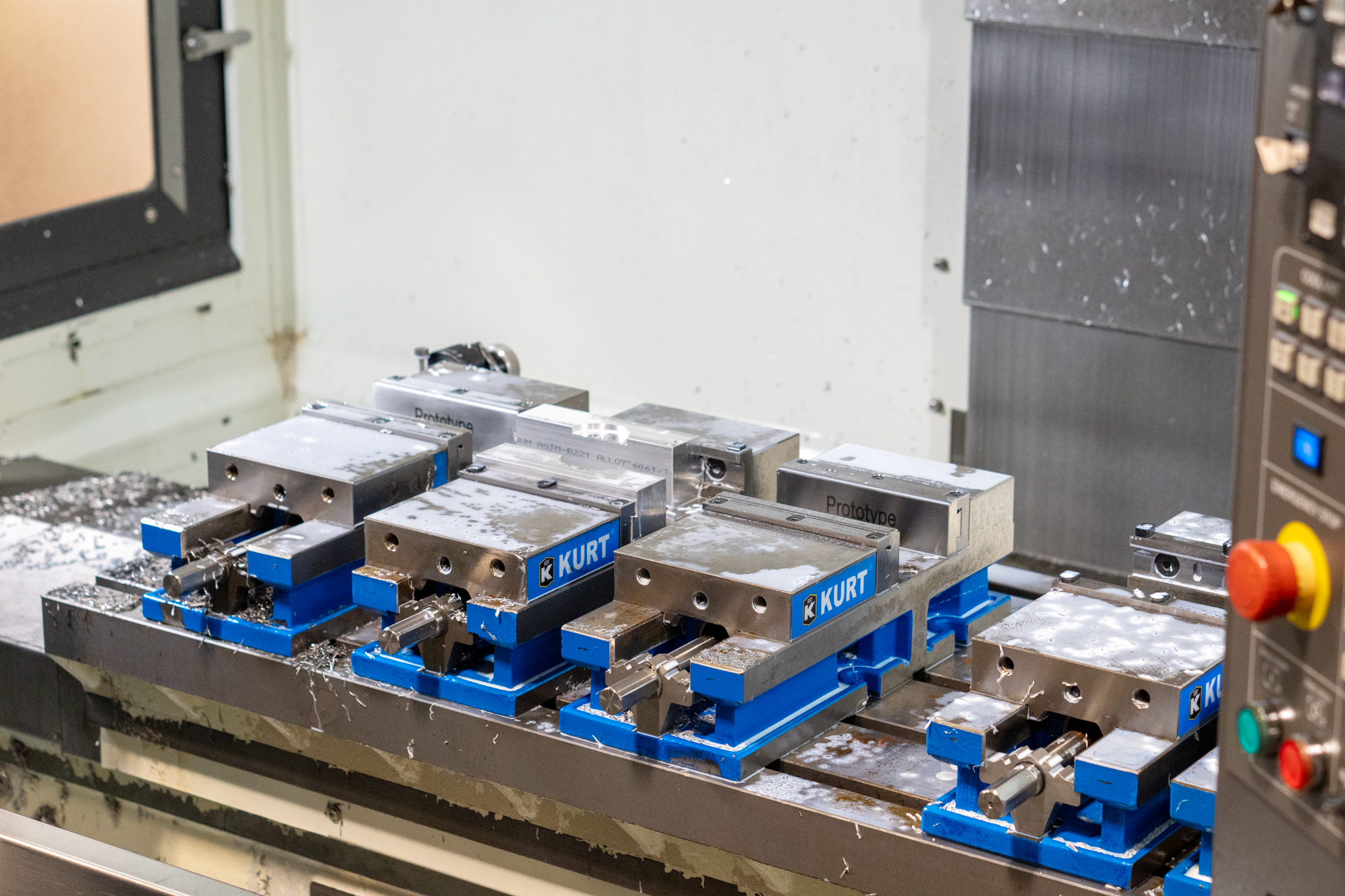
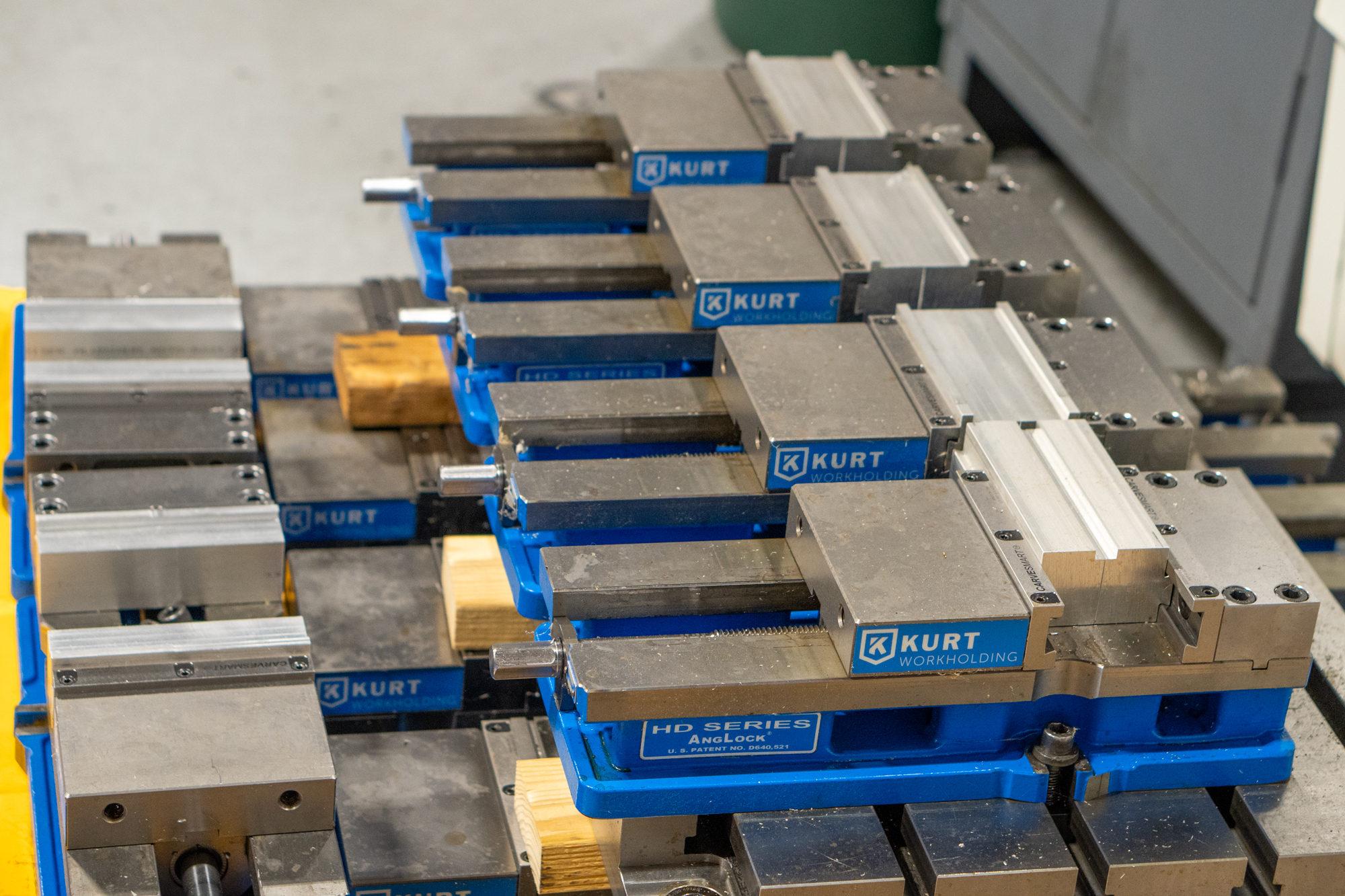
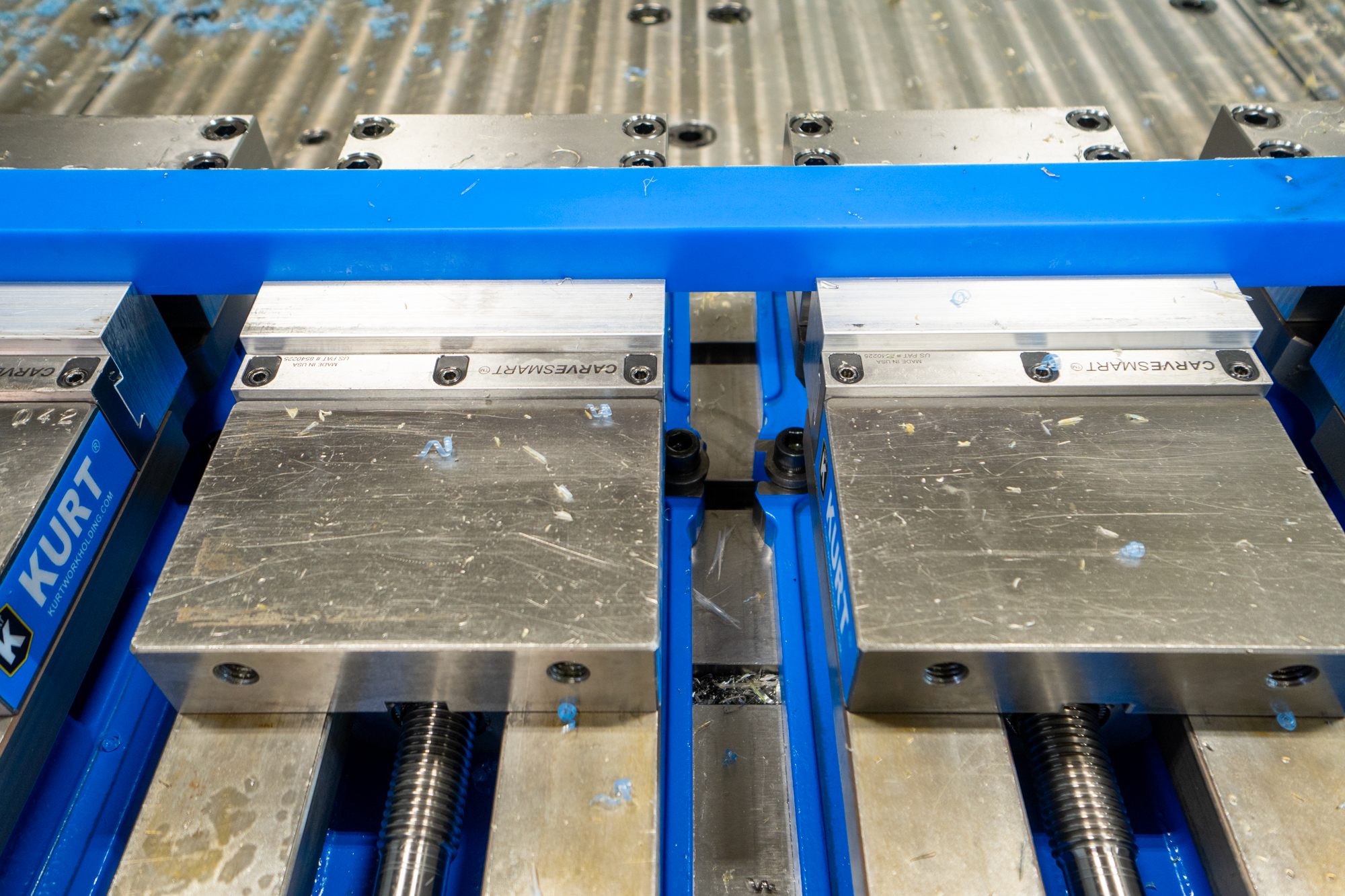
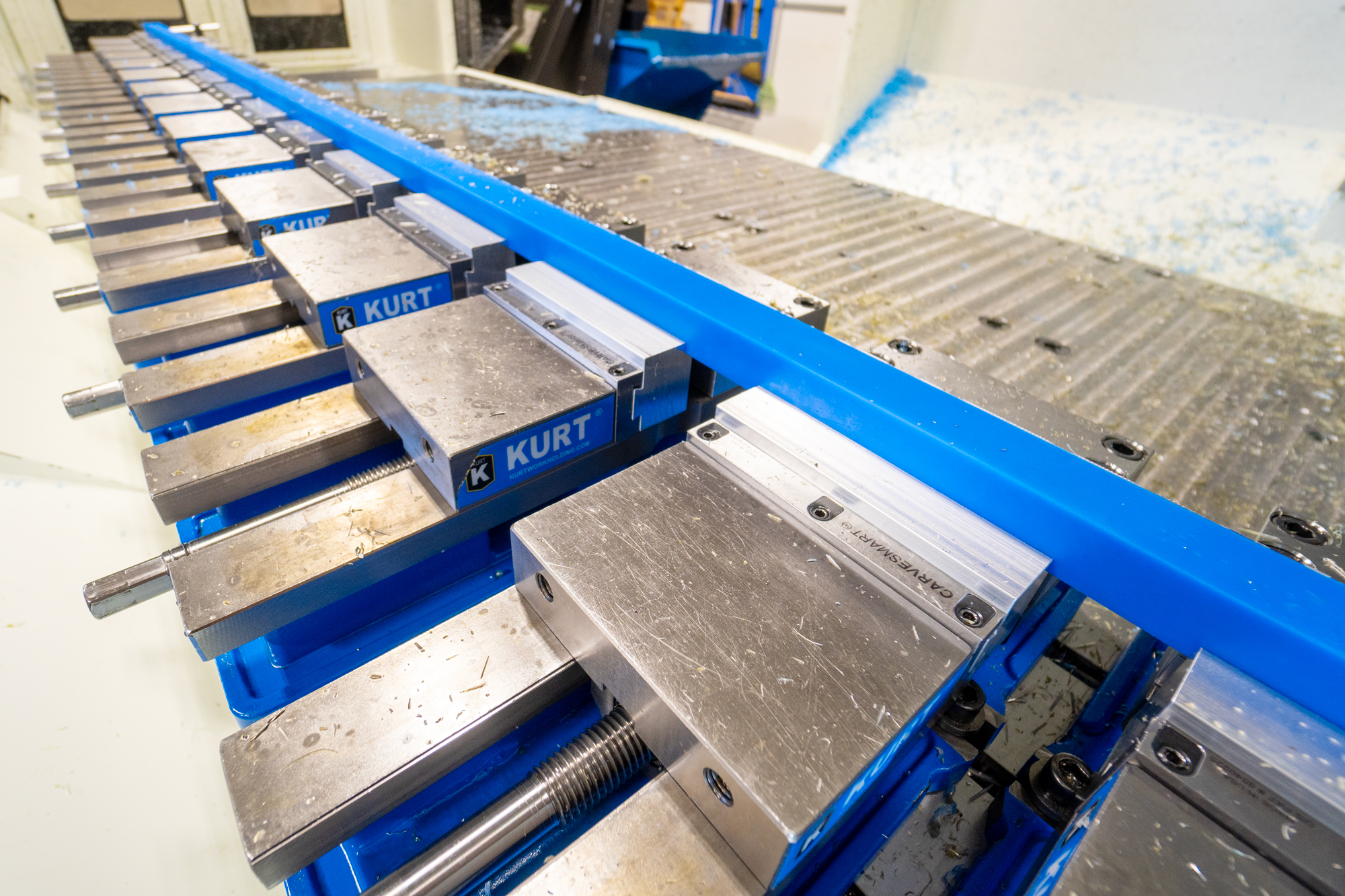
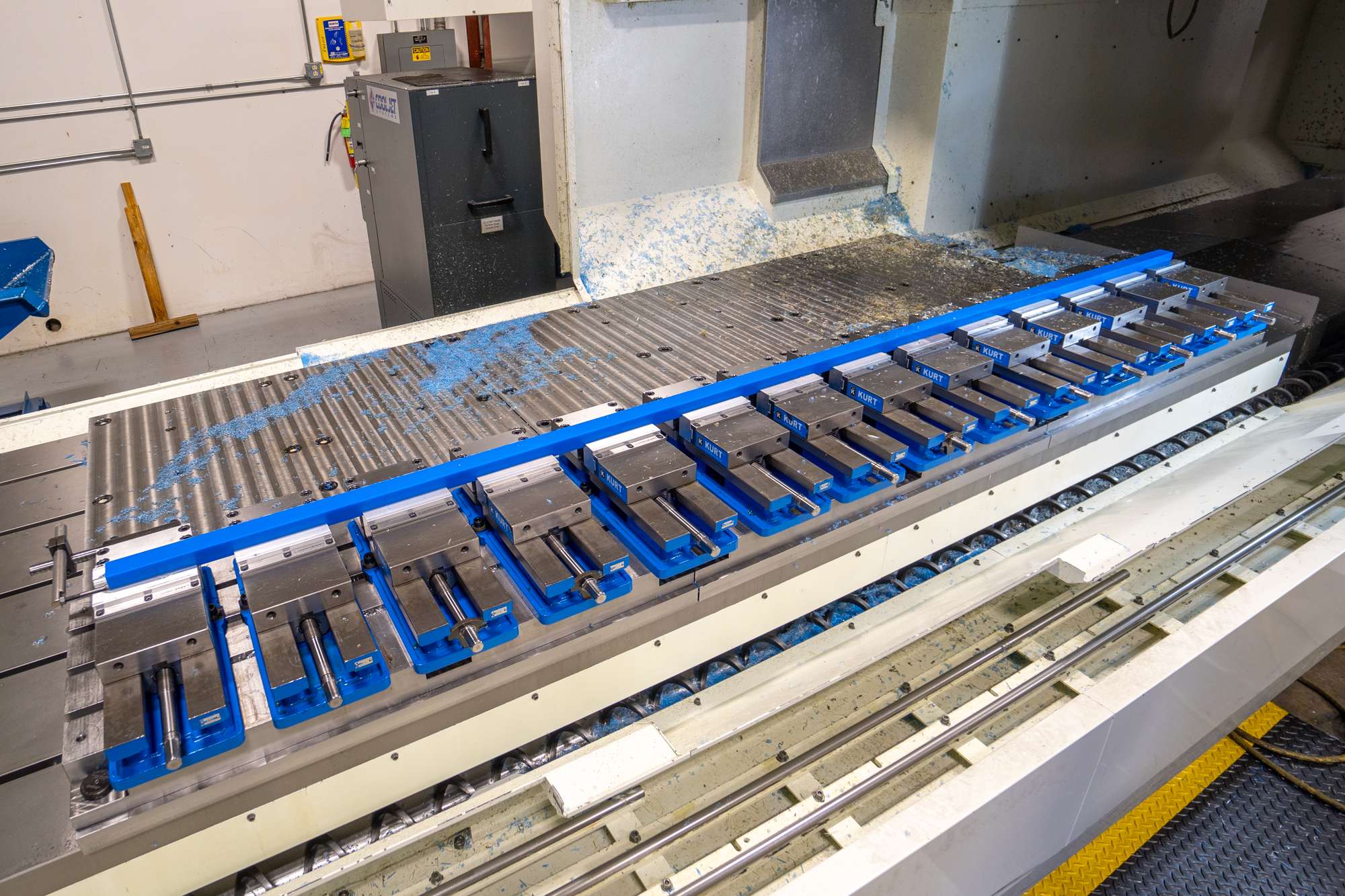
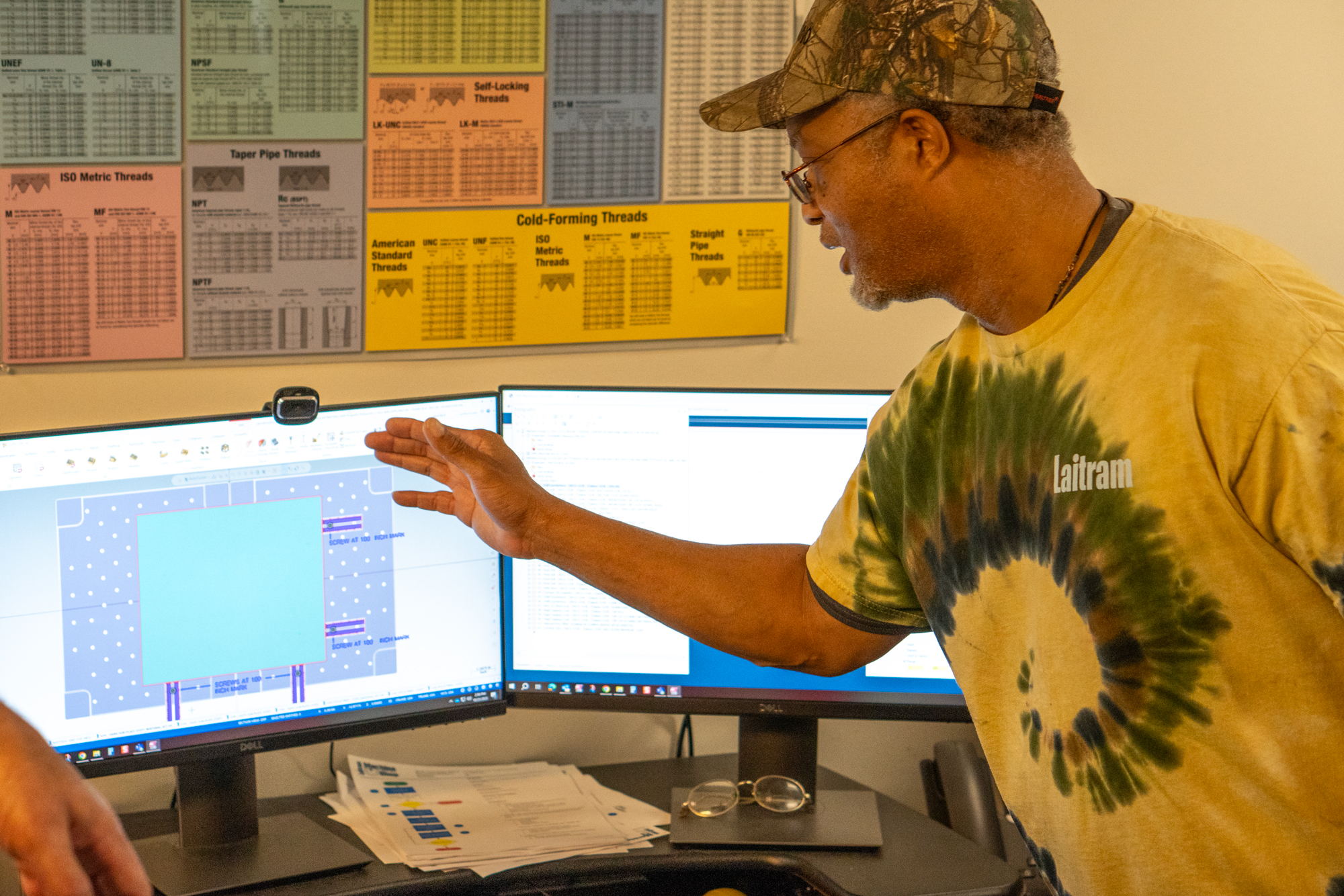
CARVSEMART Soft Jaws have an added benefit for Laitram with quick prototyping. They’re currently working on adding graduated rules to the tops of some soft jaws to make the process of setting up first operations more accurate for a wider range of machinist’s experience levels—all part of their first-part, good-part initiatives.
Laitram is testing a pair of new Kurt TriLock TL6CS vises and a the new HD690CS with integrated CARVESMART jaws. The new CARVESMART-integrated jaw option will eliminate the need to run Master Jaw Sets on Kurt vises and is also a great upgrade for their large Kurt vise fleet, since the jaws can be retrofit to the older HD690 vise model.All in all, we came away from Laitram very impressed with how they’ve optimized production and how they’re using Kurt Workholding with CARVESMART in their manufacturing processes. They’re a shining example of how quick-change soft jaws can be a game changer for companies looking to save time and money, lower waste, and foster a work environment that helps employees of all skill levels excel.